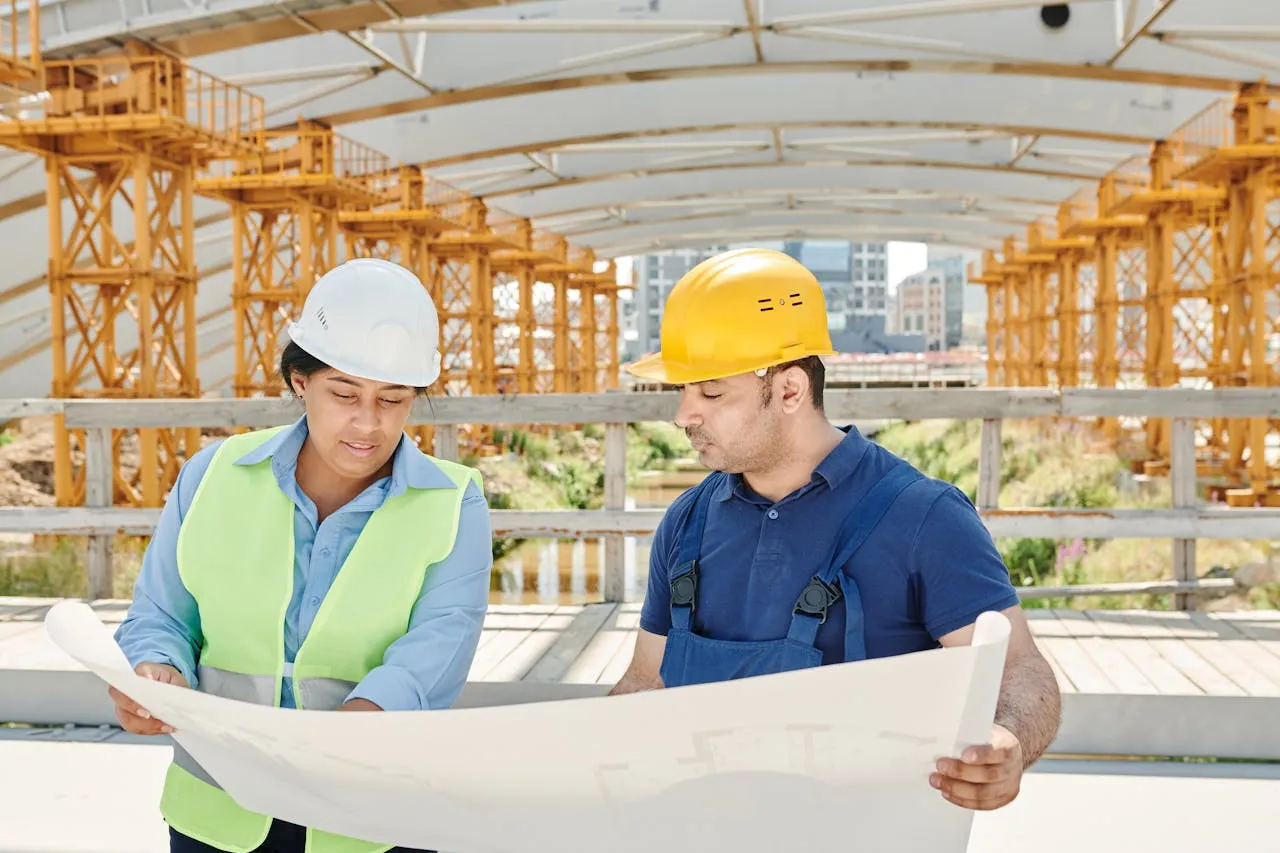
Harlan Electric and GSWC Complete Key Energized Construction Projects
Harlan Electric and Great Southwestern Construction Lead the Charge in Energized Construction In an industry where minimizing outages and ensuring uninterrupted service are paramount, Harlan Electric (Harlan) and Great Southwestern Construction (Great Southwestern) have taken bold steps to modernize how electrical infrastructure is maintained and built. Both subsidiaries of MYR Group recognized a shifting need in 2018: utilities were increasingly demanding energized construction services. This strategic insight became a launching point for significant investments in live-line barehand programs—initiatives that have since transformed their capabilities and relationships with utility partners.
Listening to the Utilities: The Call for Energized Work
By 2018, utilities across the country had begun communicating a consistent message: the future of electrical work lay in energized construction. Traditional de-energized methods, which require shutting down power lines for repairs or upgrades, created unavoidable disruptions for consumers and increased operational costs for the utilities. These factors made live-line work not just a preference but an emerging necessity.
Rather than wait for the trend to become a mandate, leadership at both Harlan and Great Southwestern took proactive steps. They listened. And more importantly—they acted.
“I went to them and said this was the direction we needed to go, I just had to show that there was absolutely a need,” explained Great Southwestern Regional Manager Ryan Little. “(President) Brandon Lark just said, ‘Make it happen,’ and we went from there.”
What Is Live-Line Barehand Work?
Energized work allows lineworkers to perform tasks on electrical systems while they remain live or “hot,” eliminating the need to take lines out of service. One standard method is hot sticking, where an insulated stick is used to handle live components from a safe distance. But live-line barehand work is far more advanced—and more challenging.
This technique involves a lineworker physically bonding to the same electrical potential as the high-voltage conductor, essentially becoming part of the energized system. To do so safely, lineworkers wear specialized suits made from fire-retardant materials and stainless-steel fibers, forming a Faraday cage. This suit allows the electrical charge to travel around the body rather than through it. The process requires deep technical knowledge, extreme focus, and flawless execution.
“It’s the mindset that comes along with it that I think separates people,” said Great Southwestern Construction Manager Tyler Mathis. “In an energized setting, there is no room for error. The planning, the technical understanding—it’s on a whole different level.”
Building Programs From the Ground Up
Neither company had an energized work program in place when they made the decision to enter this specialized field. Starting from scratch required extensive investment in both talent and infrastructure.
In Texas, Great Southwestern began by bringing on experienced personnel like Operations Manager Billy Walsh, who had more than two decades of energized work experience. The company also enlisted third-party training services and participated in train-the-trainer programs to ensure that internal knowledge could be scaled.
“It was a lot more than just putting a crew together,” Little said. “We had to take people who had never done energized work and train them to a high-performance level quickly.”
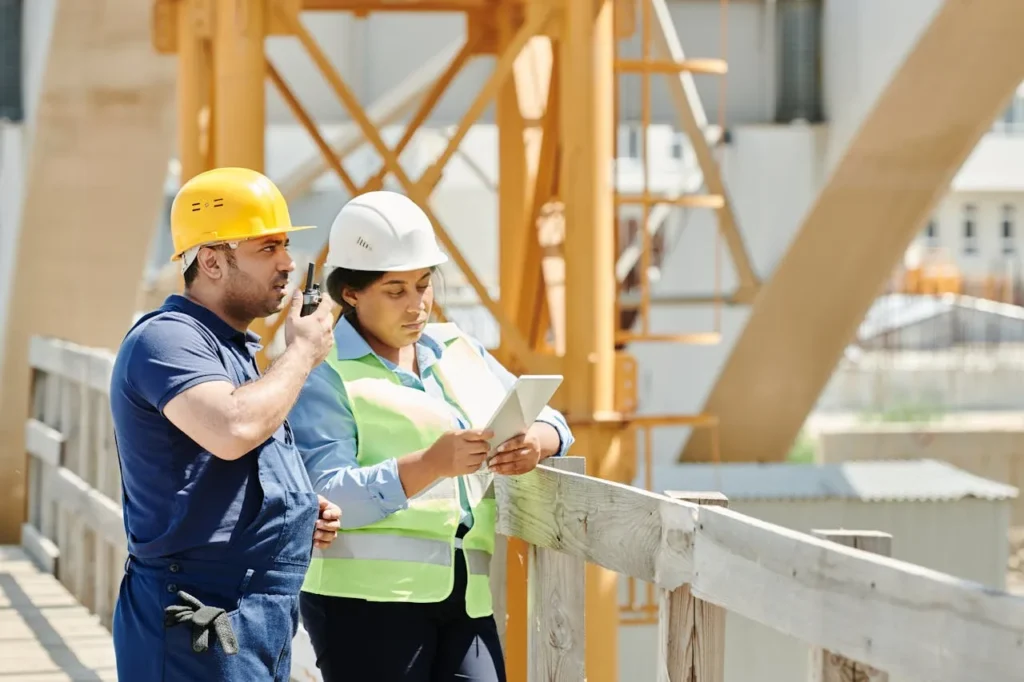
Understanding the technical demands of energized work was just the beginning. It also required shifting traditional safety paradigms. Most lineworkers are taught to maintain a minimum approach distance (MAD) from live conductors. In energized barehand work, that logic is flipped: workers must stay bonded to the conductor and remain within its electrical field at all times to maintain safety. It’s a complete reversal of instinct and training.
Harlan faced similar challenges. District Manager Chris Lenahan recalled how superintendents Mike Collins and Justin Evans were instrumental in establishing the company’s program. Yet one of the most difficult obstacles was simply finding a place to train.
“Utilities didn’t want us training on their live systems,” Lenahan explained. “So we improvised—using our New Hampshire yard, traveling to a facility in New York, and even building a custom H-frame structure inside a warehouse.”
Despite the hurdles, Harlan succeeded in certifying its first crew of 10 lineworkers in 2019. From there, the program grew steadily in size, capability, and scope.
The Creation of MYR Group’s Live Line Academy
The early challenges faced by Harlan and Great Southwestern laid the groundwork for a long-term solution: the Live Line Academy in Alvarado, Texas. This MYR Group facility now serves as a centralized training ground where lineworkers from across the company can learn energized techniques in a safe, controlled environment.
The academy offers hands-on experience across a variety of energized structures and ensures a consistent, high-quality pipeline of talent for live-line work—something Harlan and Great Southwestern had to struggle to achieve on their own when first launching their programs.
From Small Jobs to Major Rebuilds
The investment in energized construction has paid off handsomely. In just a few short years, both companies moved from small-scale work to major live-line rebuild projects.
Harlan’s early success with minor installations evolved rapidly. By the end of 2019, they were executing full 100 and 115kV structure replacements, and soon after, winning contracts for entire energized line rebuilds.
“Our customer told us that our program is the pinnacle of energized barehand programs—they hold ours as the standard,” said Superintendent Mike Collins.
Today, Harlan boasts four energized crews and more than 40 certified live-line barehand lineworkers. One standout project, the S136 Live-Line Rebuild, involves replacing 215 structures and installing 27 miles of reconductor and optical ground wire across rugged terrain in New Hampshire.
Notably, Harlan has never had an OSHA recordable incident on any of its energized jobs—a testament to the intense training and unwavering focus demanded by such work.
“It’s a compliment to our crews,” Lenahan said. “The original crew that went through our first live-line training—90% of them are still with us. Their focus on safety has allowed us to expand our workforce and maintain quality.”
Great Southwestern: A Force in West Texas
Great Southwestern’s energized journey began with 345kV transmission line work in late 2019. Since then, the company has primarily focused on 138kV lines for a major utility partner in West Texas. Their crews now perform live-line work on a daily basis, reducing customer outages while sharpening their own skills.
“There’s a lot of knowledge for this type of work here at Great Southwestern,” said Mathis. “I started with this in 2018, and the leadership team has made such a difficult aspect of the trade a seamless transition for our crews.”
Energized Work as a Competitive Advantage
Both Harlan and Great Southwestern have not only built energized programs—they’ve turned them into core strengths. These capabilities have strengthened client relationships, opened doors to new projects, and enabled both companies to elevate their lineworkers’ careers through specialized skills and leadership roles.
In the end, the story of these two companies is a testament to vision, investment, and execution. By listening to their customers, understanding the demands of the future, and committing to excellence in training and safety, Harlan Electric and Great Southwestern Construction have positioned themselves at the forefront of energized construction.