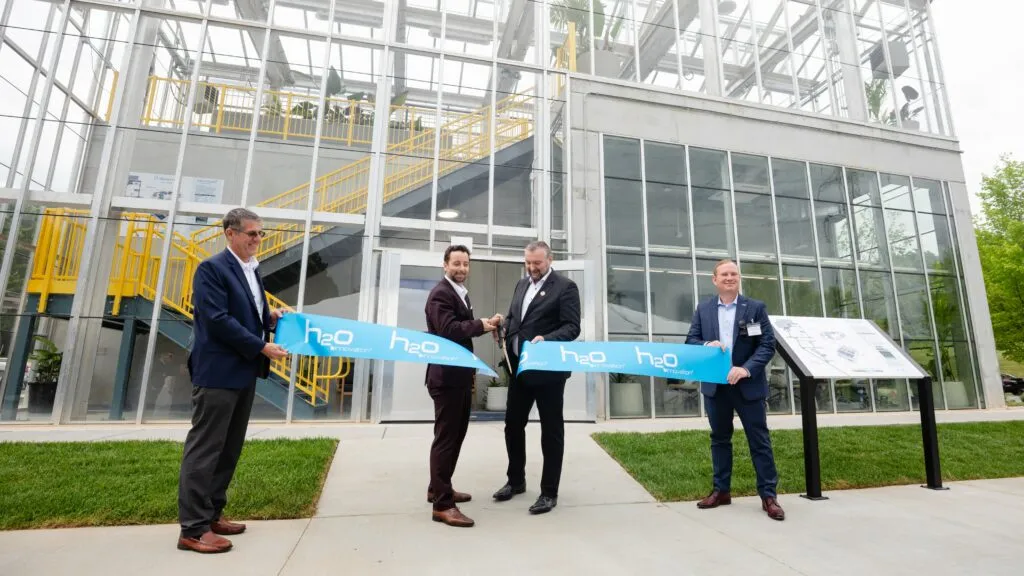
WaterHub® at Reynolds Hits Major Water‑Recycling Milestone
The doors officially opened to the WaterHub® at Reynolds’ Operations Center in Tobaccoville, North Carolina, marking a major leap forward in how heavy‑industry sites can conserve, recycle, and celebrate water. Conceived, engineered, and delivered by H2O Innovation Inc., this 5,000‑square‑foot facility is designed to recycle more than 60 million gallons of wastewater every year—enough to fill roughly 90 Olympic‑size swimming pools. The result: Reynolds expects to slash its freshwater withdrawals on‑site by about 40 percent and cut wastewater discharges by more than 90 percent, establishing a new benchmark for sustainable manufacturing in the global BAT Group and the wider consumer‑goods sector.
Blending Construction Craft and Environmental Ingenuity
Building the WaterHub® was every bit a construction project as it was a sustainability initiative. Civil crews installed a wastewater intercept and lift station that reroutes factory effluent; more than 2,500 linear feet of underground piping thread through the campus, tying the new plant into existing utility corridors. Above ground, structural steel, concrete pads, electrical gear, and process‑control cabinets support a treatment train that fuses nature‑based solutions with cutting‑edge membrane technology.
A two‑story greenhouse crowns the structure, not merely as an architectural flourish but as a living engine of the treatment process. Inside, diverse plant species partner with specialized microbiology to break down organic compounds in a low‑energy, odor‑free environment. Downstream membrane filtration and advanced disinfection polish the water to reclaimed‑quality standards, ready for non‑potable reuse throughout the facility.
How the Hybrid Treatment Train Works
- Primary Capture and Conveyance
Wastewater Intercept & Lift Station – Influent from production lines is intercepted before entering the municipal sewer. Pumps elevate flows to the headworks of the WaterHub®, eliminating hydraulic bottlenecks without expanding the factory’s footprint. - Eco‑Engineered Bioreactor
Greenhouse‑Based Fixed‑Film Biology – Rows of planted media deliver both aesthetic and functional benefits. Root zones create a vast surface area where biofilms form, metabolizing biochemical oxygen demand (BOD) and nutrients. Natural sunlight drives photosynthesis, lowering mechanical aeration requirements.
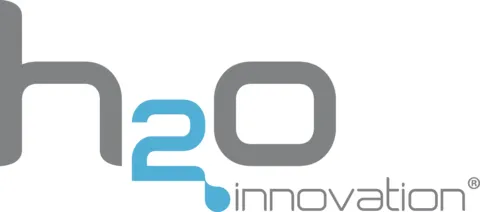
3. Membrane Filtration
Ultrafiltration Skids – Hollow‑fiber membranes provide a physical barrier to pathogens and suspended solids, protecting downstream assets and ensuring a consistently high‑quality ffluent, even during peak factory production cycles.
4. Final Disinfection
UV & Optional Chlorination – Ultraviolet reactors deliver log‑level reductions in bacteria and viruses without chemical by‑products. A trim dose of chlorine can be applied when long distribution lines or storage tanks make residual protection prudent.
5. Water Reuse & Site Integration
Process Loops & Landscape Irrigation – Treated water is piped back into the plant for cooling towers, utility makeup, and cleaning operations. Surplus flows irrigate the site’s new 1,300‑square‑foot native garden, itself planted with more than 400 individual specimens across 24 species to enhance biodiversity.
Construction by the Numbers
Metric | Quantity | Significance |
---|---|---|
Facility Footprint | 5,000 ft² | Compact scale minimizes land take. |
Underground Piping | 2,500 linear ft | Ties new plant to legacy utilities without major disruption. |
Annual Water Recycled | 60 million gal | ~165,000 gal every day of operation. |
Reduction in On‑Site Freshwater Withdrawal | ≈40 % | Direct hit on corporate water‑intensity KPIs. |
Reduction in Wastewater Discharge | >90 % | Eases pressure on municipal treatment and local waterways. |
A Sustainability Showcase, Not a Hidden Utility
While many wastewater plants are tucked behind security fencing, the WaterHub® invites employees and visitors to witness the water cycle in action. The greenhouse’s glass façade, natural lighting, and ambient planting blur the line between process equipment and botanical garden. Interpretive signage explains each treatment step, and viewing walkways offer safe, elevated vantage points. The intent is as much educational as operational: to foster a shared culture of water stewardship across the Reynolds workforce and its community.
Outside, the native garden doubles as a living laboratory for pollinators and a test bed for drought‑tolerant landscaping. Because the garden relies entirely on reclaimed water for irrigation, it frees additional potable supply for local residents and demonstrates closed‑loop resource thinking.
Alignment with the BAT Group’s Global Water Ambitions
Reynolds’ parent company, BAT, has publicly committed to reducing water withdrawn across its worldwide facilities. By activating the WaterHub®, Reynolds alone projects a 6 percent dent in the Group’s total water intake. That single‑site impact underscores how localized infrastructure can drive portfolio‑wide environmental wins.
Innovation in Service of Resilience
For H2O Innovation, the Reynolds project encapsulates its philosophy: tailor solutions that marry performance, aesthetics, and ecological sensitivity.
“The WaterHub® is a prime example of how innovation can advance both sustainability and resilience,” noted Guillaume Clairet, Chief Operating Officer at H2O Innovation. “By supporting partners like Reynolds in conserving water and achieving their environmental goals, we’re proud to play a role in their journey toward water positivity. Together, we are not only conserving water but also redefining how industries can operate sustainably in harmony with the environment.”
Beyond the numbers, the plant provides a hedge against drought and water‑price volatility, ensuring that production capacity is decoupled from municipal supply constraints. It also positions Reynolds to meet tightening regulatory expectations and consumer scrutiny around environmental footprint.